This website uses cookies for a better browsing experience.
If you agree to the use of cookies, please click the "Agree" button.
Please refer to the Privacy Policy regarding the use of cookies on this site.
Our Engineering DNA
Contributing to society through technology
The first company in Japan to offer oil-less bearings, Oiles is a pioneer in Seismic Isolators and vibration control devices, and a manufacturer of window opening/closing devices for air ventilation and smoke exhaust for safety in daily life. Over the 70 years since our founding, we have continuously provided products and technology that offer solutions to challenges faced by society. Lying at the origin of this is the path taken by our predecessors, each of whom has always taken on the challenges presented by research and development, starting with the founder of Oiles. To take the company forward and work toward sustainable growth ahead of the centenary of our founding, the DNA of human resources to sustain and ultimately reform our R&D activities that are the source of our innovation is essential. Here we look at some of the employees who light up the future of Oiles.
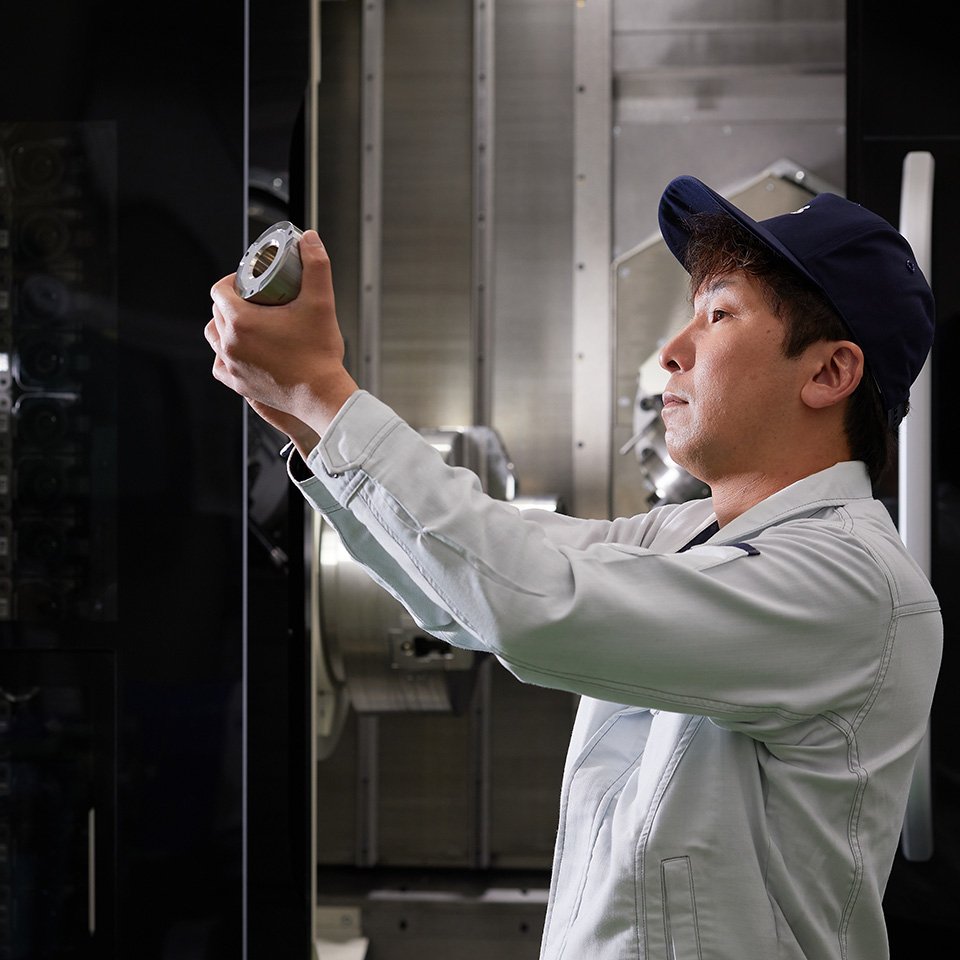
Refine
Oiles Air Bearings (OABs) boast the highest level of precision among all Oiles products. The most significant difference between these and plain bearings and roller bearings is the fact that they are contactless. This means no wear occurs, and friction resistance is as close as possible to zero, and gives them the highly-desirable characteristic of rarely needing to be replaced. They can even be manufactured in various shapes and offer customized performance in other ways to meet customer needs.
Oiles Air Bearings combine different materials, which means any deformation in a bearing being machined is significant, and thus it is challenging to ensure precision. They are produced in a temperature-controlled room where the temperature is maintained at a set level. Still, to achieve micron-order finishing, differences in cutting fluid and measuring instrument temperatures, room temperature and even changes in tool sharpness are taken into account to ensure accuracy for each machined bearing. By putting in place a thorough system with many processes in this way, the result is Oiles Air Bearings (OABs) of the highest precision. While the fact that all processes depend on the other processes presents a challenge, I think this challenge is very interesting. I also believe that it is my responsibility to help the company pass on its technology and machining expertise in production to future generations. So I take plenty of time to work on human resources development.
Carefully picking out and addressing comments made both inside and outside the company such as “I wish this kind of product was available” or “there is no such product on the market so let’s just give up” results in trust and confidence, and giving my all to adapt products to fit the customer’s needs is what gives me satisfaction in my work.
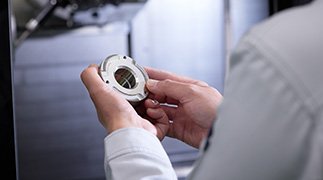
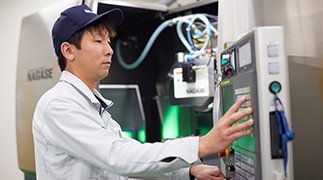
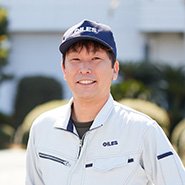
Mr.Sato
Oiles Air Bearings Group, Production Sec. 3, Fujisawa Plant, Production Division
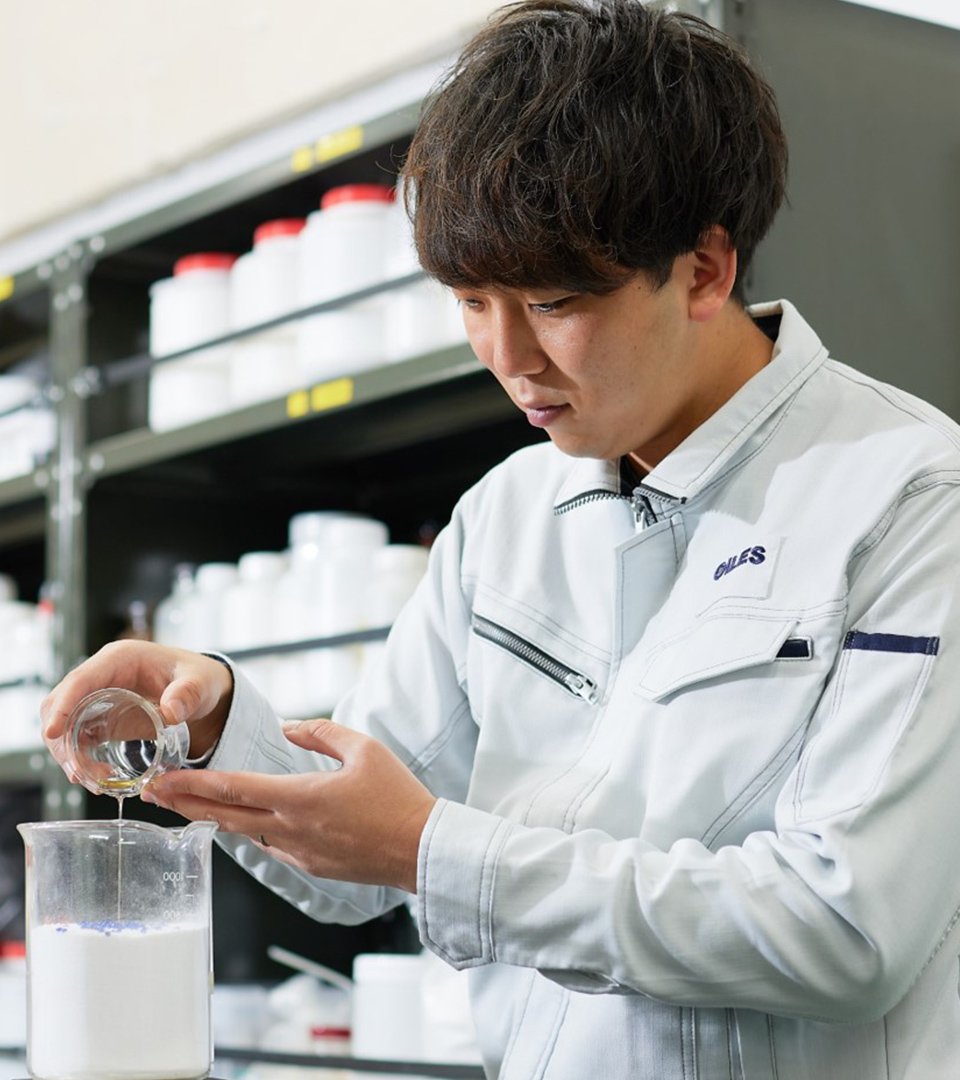
Master
I am currently working on developing plastic bearings for electric vehicles (EVs).
The automobile industry is currently going through a once-in-a-century period of transformation as typified by CASE and MaaS, and to accelerate the widespread adoption of electric vehicles will require reducing their weight and heat management to resolve the challenges related to their driving range. I am in charge of developing plastic bearings that meet such needs and offer low energy transmission loss (friction) while suffering only minimal effects from heat.
Our Research & Development Department is in charge of a wide range of activities, from prototyping to testing, analysis and mass production. To make the plastic bearings that I am in charge of, we use the three processes of adding additives to powdered or granulated plastic materials, then mixing, melting and kneading the material, before molding it (pouring it into a mold and cooling it to solidify it). It is kind of like making chocolate. There are countless types of materials; even a slight difference in the blend or way they are made can change the finished product. This gives the work a lot of depth and makes it very interesting. I clearly remember how impressed and excited I was when I first saw plastic in a melted state after joining the company.
“All truths are easy to understand once they are discovered; the point is to discover them.”I really like this quote from Galileo Galilei.
Often in R&D, things do not go as planned and phenomena occur that you don’t understand. In such situations, you can gradually understand the situation by repeatedly going through the cycle of hypothesizing and verifying. This then becomes expertise, and leads to discoveries. Such new discoveries are what make research so deeply interesting, and they lead to the development of one-of-a-kind products. We have also been able to identify regularities from a range of hypotheses in our current development work, and last year we were able to apply for three patents as world-first discoveries.
Bearings are referred to as the “bread-and-butter of the machinery industry” and are general-purpose elementary components that are always used in any machine with rotating parts. With the target of widespread use of products I have worked on the development of, I will stay curious about everything and exercise rich creativity in R&D.
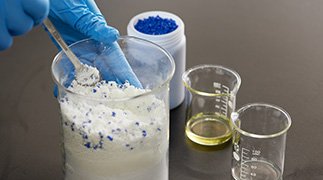
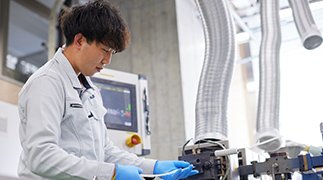
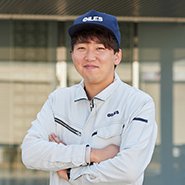
Mr.Takechi
Research & Laboratory-2, Research & Development Dept.
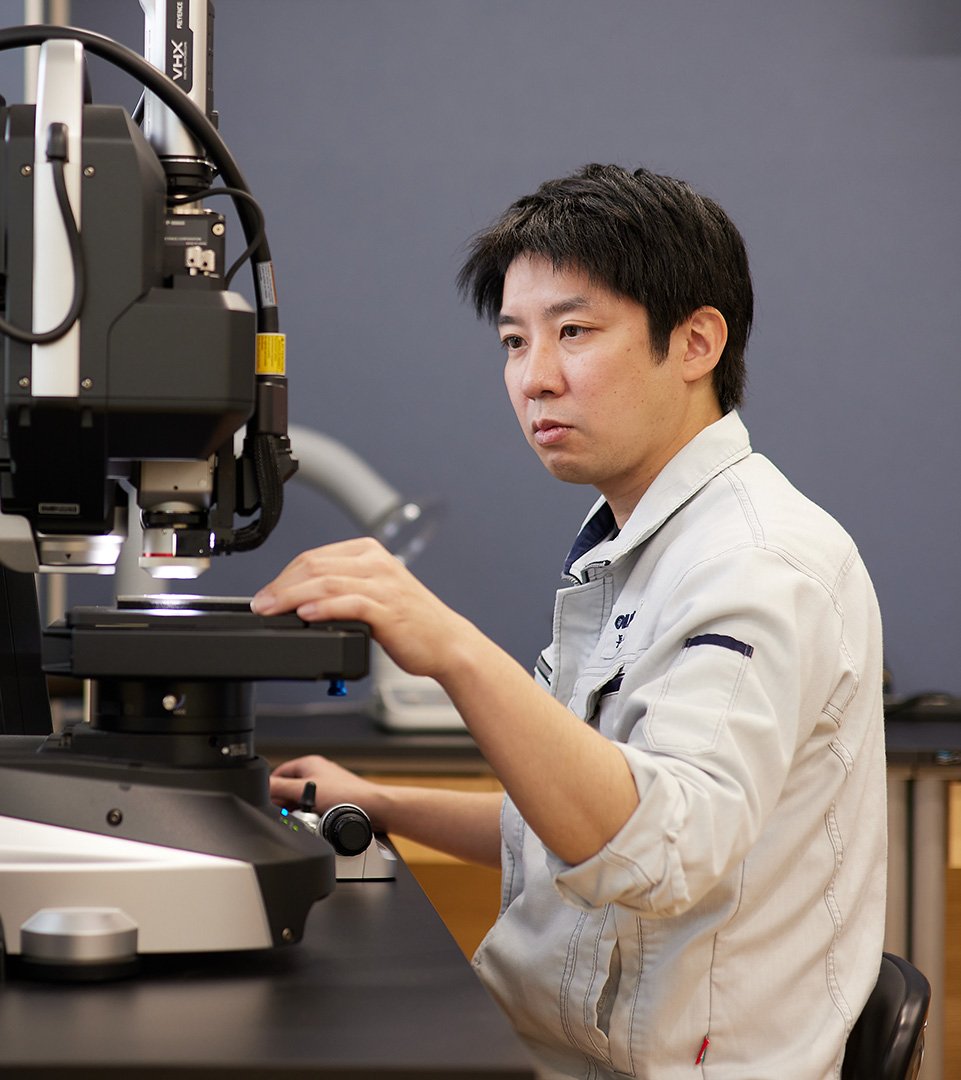
Use
The seismic isolators that Oiles develops are composed of numerous materials, with more oversized products measuring 1.6 meters in diameter and weighing two tons. As such, multiple divisions work together to create and test prototypes and undertake development. In R&D, we investigate the properties that would make the ideal device to achieve safe and secure buildings, and undertake repeated simulations and experiments to make this a reality. We go through a repeated cycle of manufacturing and evaluating our test samples, and I feel exceptional enjoyment when the envisioned characteristics are achieved.
However, R&D is also difficult because you can sometimes overlook important elements if you are too convinced by an assumption you have made. So you must make objective judgments while still having firm confidence and belief.
This way of thinking accompanies me when I embark on on-site surveys of areas hit by large earthquakes. Whenever I hear people say that their seismically-isolated building suffered no damage and was able to continue to fulfill its functions immediately after the earthquake or that they hadn’t even noticed there was a large earthquake, this directly gives me a sense that people’s lives and the safety of buildings are being protected. This is the moment when the ideal we pursue in R&D changes to firm belief in real life.
While feeling the joy of contributing to society through R&D that incorporates the voices of those on the ground, I also strongly feel that we must continue to refine our technology to minimize the damage from earthquakes and undertake the development of products that the market will accept.
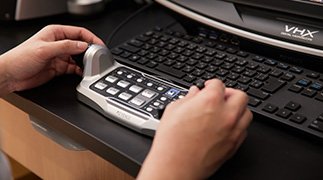
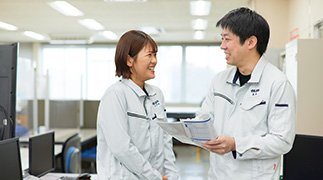
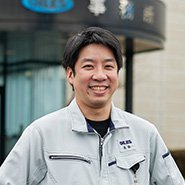
Mr.Nagahiro
Development Sec., Engineering & Design Dept., Damping & Isolation Division